Our product
1- CHEMICALS
MDI
Polyurethane binders based on polymeric MDI (PMDI) are used in many applications. They are particularly suitable for the production of engineered lumber. MDI enables the production of high-quality and emission-free chipboard, OSB and MDF, thus conserving precious natural resources. MDI can also be used to bring recyclable materials such as polyurethane rigid foam and agricultural materials like straw “back to life”. In addition, MDI is used as a binder for foundry sand and for rock consolidation in mining.
Polyols
Polyurethanes are one of the most versatile plastic materials. The nature of the chemistry allows polyurethanes to be adapted to solve challenging problems, to be molded into unusual shapes and to enhance industrial and consumer products by adding comfort, warmth and convenience to our lives.
Polyurethanes are formed by reacting a polyol (an alcohol with more than two reactive hydroxyl groups per molecule) with a diisocyanate or a polymeric isocyanate in the presence of suitable catalysts and additives. Because a variety of diisocyanates and a wide range of polyols can be used to produce polyurethane, a broad spectrum of materials can be produced to meet the needs of specific applications.
Features
Binder of choice to achieve strength properties
Bonding of emission-free wood based panels
Suitable for a wide range of products and applications like OSB, Particleboard, MDF and Wood Fiber Insulation Boards
On the basis of applications:
Flexible Foam
Rigid Foam
Others (Adhesives, Sealants, and Elastomers)
Polyester Polyols
A polyester polyol is a polyol used in polyurethane production that is saturated and has terminal hydroxyl groups.
Polyester polyols are used to make both rigid and flexible polyurethanes. They tend to be more expensive than polyether polyols and are also more viscous at the same temperature as a polyether polyol would be. Additionally, polyester polyols are more easily attacked by moisture and broken down, so they are only used in applications where the physical properties that they can give to the polyurethane are needed.
Common Applications• Acrylate polymerization
• Automotive (NVH) Noise, Vibration, Harshness
• Non-foaming emulsions
• Polyurethane surface coatings
• Recreational vehicle adhesive
• Adhesion additive
• Fiberglass reinforced backing material
• Manufactured housing adhesive
• Sealer insulation (one-component foam


2- MACHINES
SANDWICH PANEL LINE
Rigid polyurethane foam has the lowest thermal conductivity of all insulating materials and is therefore used in the form of metal composite elements in industrial and cold store construction, as well as in cooling chambers for supermarkets and in thermal assemblies for trucks. With its highly developed, continuously or discontinuously operating sandwich panel lines, HENNECKE-OMS has played a decisive role in this success story right from the start. The PANELMASTER STEEL plant is designed for the continuous production of top-quality sandwich panels with different facings, panel thicknesses and profiles and the option of a core structure made of polyurethane or mineral wool. Thanks to the company HPT GmbH, the HENNECKE GROUP also has a highly-specialized provider of high-performance trapezoidal sheet roll forming systems, which can be seamlessly incorporated into the existing plant concept for the PANELMASTER STEEL continuous sandwich panel lines. In the continuous production of sandwich elements with metal facing, HENNECKE-OMS is one of only a few suppliers that can offer its customers convincing all-round solutions from a single source.
Profile
The entry section contains the equipment for handling the coil and processing the metal facings. This includes unwinding and feeding the steel coils into the plant, preparing the strips by trimming and connecting them, as well as the profiling of the lower and upper metal facings. The surface and edge profiling gives the sandwich composite elements a defined shape and joins them securely together.
The profiling section usually comprises the following parts:
▽ Facing infeed
▽ Lining


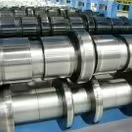

Mixing and Metering
HENNECKE-OMS offers the entire equipment for the metering, storage, transport, and monitoring of raw materials and additives The polyurethane metering machines are responsible for the homogenous mixing of the reactive components polyol and isocyanate, as well as various additives (e.g. catalysts, blowing agents, curing agents, flame retardants). HENNECKE-OMS sandwich panel production lines are based on a well-planned arrangement of the individual units and top-quality components. This guarantees the user a uniform cell structure and an efficient raw material yield.
The raw material dispensing equipment, or wet part, usually comprises the following:
▽ Metering units
▽ Dynamic premixing station and gas loading system:
▽ Mass flow meter
▽ Temperature control unit and cooler
▽ Tank farm




The center section
The center section for continuous metal facings is the heart of a PANELMASTER STEEL production line. It represents our company’s accumulated expertise in polyurethane processing under high pressure.
The center section of the PANELMASTER STEEL usually comprises the following:
▽ Preparation for foam application
▽ Foaming portal
▽ Mixhead
▽ Double plate conveyor
▽ Temperature control unit
▽ Band saw
▽ Infeed for mineral wool panels




Plant control system
art, computer-aided electronic systems ensure maximum operating safety, require minimal space and allow product changes to be implemented quickly and virtually automatically.
The plant control system usually comprises the following parts:
▽ Panel management system
▽ Process data acquisition
▽ Graphical evaluation and analysis


Cooling and stacking
This so-called cooling zone provides for the interim storage and cooling of the panels. Here the panels are finished and stacked, interlayers are inserted and the stacks are wrapped with a protective film.
The cooling and stacking of the PANELMASTER STEEL usually comprises the following parts:
▽ Cooling line
▽ Milling station
▽ Stacking station
▽ EPS / XPS plate infeed



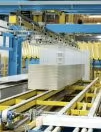
3- Prepainted Steel Coil
Prepainted Steel Coil
The substrate of the Prepainted Steel Coil is a cold rolled substratea hot-dip galvanized substrate and an electrogalvanized substrate. The coating types can be divided into polyester,silicon modified polyester,polyvinylidene fluoride and plastisol.The surface state of color-coated steel sheets can be divided into coated sheets.embossed sheets and printed sheets.Color-coated steel sheets are widely used in construction appliances and transportation industries. For the construction industry,they are mainly used in steel structures,airports,warehouses and freezers. For roofs and doors of industrial and commercial buildings,there are fewer color steelplates for civil buildings.It differs from plastic steel in the composition of the material. The magnet can be sucked.
Product Details
The substrate of the color coated steel plate is a cold rolled substratea hot-dip galvanized substrate and an electrogalvanized substrate. The coating types can be divided into polyester,silicon modified polyester,polyvinylidene fluoride and plastisol.The surface state of color-coated steel sheets can be divided into coated sheets.embossed sheets and printed sheets.Color-coated steel sheets are widely used in construction appliances and transportation industries. For the construction industry,they are mainly used in steel structures,airports,warehouses and freezers. For roofs and doors of industrial and commercial buildings,there are fewer color steelplates for civil buildings.It differs from plastic steel in the composition of the material. The magnet can be sucked.
▼ Specifications and features:
1.Light weight : 10-14 kg/square meterequivalentto1/30 of the brick wall
2.Thermal insulation : Thermal conductivity ofcorematerial: λ<=0.041w/mk
3.High strength : It can be used as a load-bearing structure for ceilings,bending and compressiongeneral houses do not use beams and columns.
4. Bright color : no need for surface decorationcolor galvanized steel anti-corrosion layer is maintained for 10-15 years.
5.Flexible and quick installation : the construction period can be shortened by more than 40%.
6.Oxygen index : (OI)32.0(provincial fire protection product qualityinspection station)
4- Galvanized/Galvalume Coil
Galvanized/Galvalume Coil produced by our company is coated with a layer of zinc as the main rawmaterial on the surface of the cold-rolled sheet. Galvalume Coil is widely used in building materials decoration(composite panelsqlass tiles,rolling doors),daily necessities (washing machines, refriaerators.
ovens).And packaging containersetc.
The company has excellent equipment configuration and strong technical force.It can produce galvanized steel sheets of various specifications ranging from 0.10 to 1.20x700~1250 xC.The ultra-thin large zinc galvanized sheets produced by 0.10~0.151000xC are at the international ad-vanced level. The domestic gap has an incomparable advantage
5-Hot Rolled Steel: The Process and Its Implications
Hot-rolled steel undergoes a process where it's rolled at a temperature higher than its recrystallisation temperature, generally over 1000˚F (537.778°C). This high temperature allows the steel to be shaped and formed more freely, facilitating larger quantities of steel production.
However, as the steel cools down, it shrinks non-uniformly, leading to less precise shapes and sizes. While this might be a disadvantage when precision is paramount, hot-rolled steel is ideally suited for applications where such factors are not a top priority, such as structural steel components like beams and railroad tracks.


6- SANDWICH PANEL
A: PUR B: PIR